兴起于20世纪90年代的内蒙古自治区乌兰察布市铁合金产业,一度因生产粗放被外界贴上“黑大粗”标签。记者近日来到乌兰察布市看到,多年来坚持不懈进行绿色转型,这里的铁合金产业实现“脱黑向绿”,目前年产值已突破800亿元,成为全国产量最大的铁合金生产地级市。
走进绿树环抱的内蒙古吉铁铁合金有限责任公司,微风吹过,花草的清香扑鼻而来。“公司生产铁合金产品的同时,每年利用所产生的近6亿立方米电炉尾气代替天然气,可年产10万吨大规格超高功率石墨电极以及17.5万吨甲醇产品,既实现了碳捕集和碳中和,又进一步延长了产业链。”公司董事长郭军说。
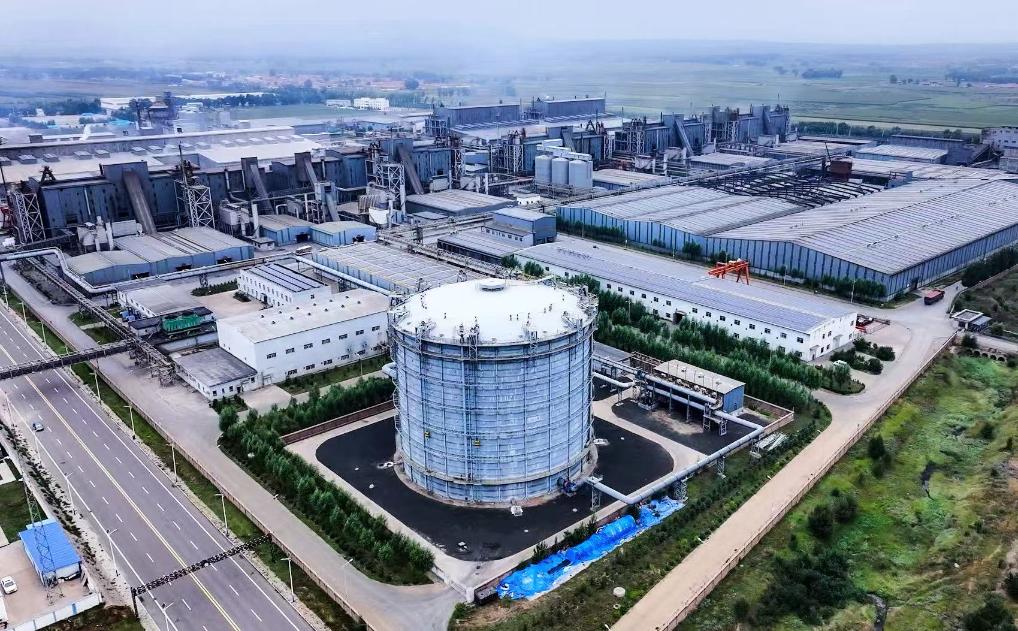
吉铁铁合金公司的发展案例代表了乌兰察布市一批铁合金企业发展方式、发展理念之变。铁合金产业过去是公认的高耗能产业,特别是矿热炉未封闭、煤气放散“点天灯”等现象,成为当地铁合金产业可持续发展的重大挑战。
在国家“双碳”目标引领下,2021年在前期转型基础上乌兰察布市以壮士断腕的决心,对铁合金产业全面实施“三个一批”和“五化改造”行动,即淘汰退出一批、技改升级一批、延链强链一批和除尘密闭化、能耗值标杆化、资源循环利用化、智能化、绿能化。不断推进的产业转型升级,让铁合金产业发生了从粗放到精细、从低端到高端的蜕变。
乌兰察布市副市长于海成介绍,过去,铁合金行业均为交流冶炼,与直流炉冶炼工艺相比,存在能耗高、负荷调节能力差等问题。为此,乌兰察布市组织本地企业联合国内科研院所、高校、设计单位和设备制造厂商,积极推进直流冶炼技术的研发。
经过近2年的研究,内蒙古景蕾实业有限公司2024年转化应用“直流矿热炉冶炼技术”,成功建成大容量、全密闭的埋弧式直流冶炼锰硅合金矿热炉,使单位电耗下降10%至15%,焦炭消耗减少10%左右,企业生产成本明显降低。
在内蒙古佰特冶金建材有限公司,一辆辆满载岩棉和矿棉的货车不时驶出企业。该公司进行资源循环利用,每年将生产铁合金产生的24.5万吨尾渣,通过冷渣子高温融化方式生产岩棉、热渣子热装热兑方式生产矿棉,并将生产铁合金的余气余热进行发电。
“2024年,光尾渣制棉和余气余热发电年产值就超1亿元。”公司总经理杨立均说,走好绿色低碳之路,非但没让企业感到负重前行,发展后劲反而越来越足了。
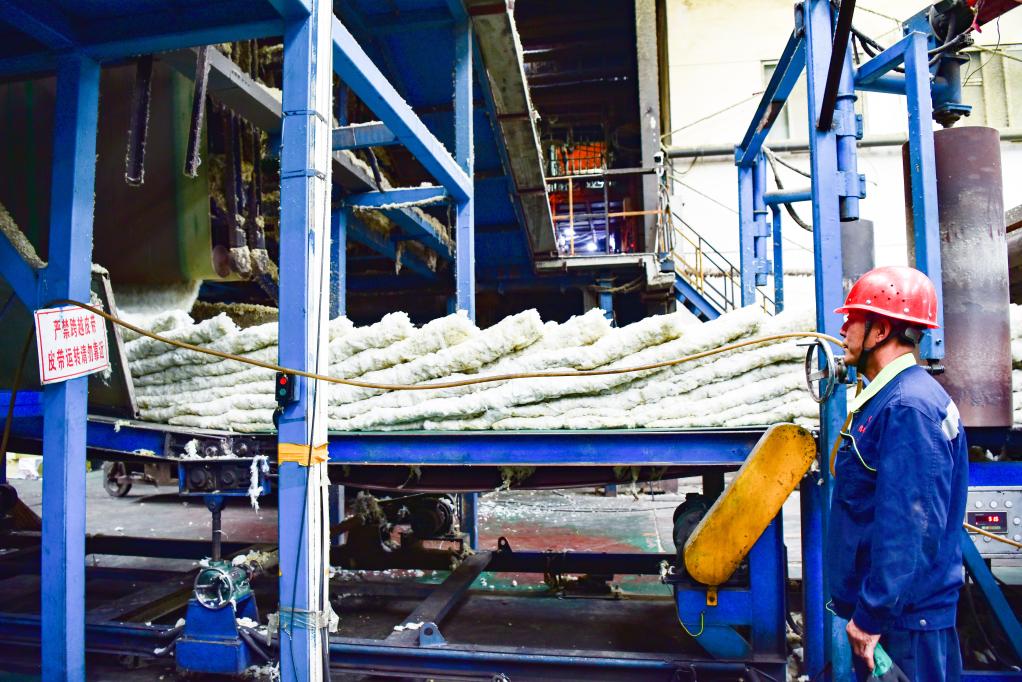
乌兰察布市工业和信息化局的数据显示,仅2021年和2022年,“三个一批”和“五化改造”行动就带动技术改造投资约40亿元。2021年以来,有152万吨落后产能退出,铁合金企业数量由91家优化到58家……
于海成说,经过近些年的转型升级,全市铁合金能效标杆以上产能比例达到60%,余气利用、废渣综合处置率均达到100%,新建项目绿电占比超60%。他说:“2024年,全市铁合金总产量达1132万吨,产值超过800亿元,带动1.8万人就业。”
在“求绿”的过程中,地方和企业均尝到了甜头,铁合金产业更加坚定走好生态优先、绿色发展为导向的高质量发展新路子。在兴和县,总投资25.6亿元的铁合金绿色供电项目于4月15日启动建设,未来可通过绿电供应降低生产成本,同时减少碳排放。
“铁合金既是乌兰察布市的传统产业、优势产业,也是未来的核心和支柱产业。”于海成说,“乌兰察布市将发挥新能源资源丰富的优势,探索无碳冶炼等新技术、新工艺,逐步把铁合金产业打造为低碳、零碳产业,让绿色低碳成为乌兰察布铁合金产业高质量发展的鲜明底色,向着千亿元产值进军。”(记者王靖)